If you have ever modeled a climbing wall you know how time consuming even small changes can be. Most people use Sketchup to design climbing walls for two simple reasons: 1. it’s free and 2. it allows moving corners within their deegree of freedom. Add a triangle whenever you’re stuck since triangles are always planar…
I’m using Rhino and I prefer large polygons with as few sharp corners as possible. Here’s how I do it:
Use the category filter “Walls” to see all of my wall design related projects.
I’m currently available for new design projects. Please contact me by e-mail.
The surface of most climbing walls made of plywood. Sheet sizes differ but common dimensions are 1.5 x 1.5 m, 2.4 x 1.2 m, 2.5 x 1.25 m and 3 x 1.5 m.
Hole patterns are either “orthogonal” and parallel to the panel edge or 45° rotated which is called “diamond grid”. Some wall manufacturers also use a triangular hole pattern, however I don’t think it makes much sense at all. The height and with of an equilateral triangle are not the same, hence it is impossible to create a seamless pattern on squares and rectangles with an aspect ratio of 2:1
A modern climbing walls might not have M10 t-nut holes on all surfaces anymore. Yet I’m convinced that rendered images of climbing walls with panels, holes ans maybe even holds are easier to understand than blank surfaces.
And yes, if it was just for renders, one could use textures to simulate holes and beveled paneld edges. M10 t-nut holes could be created with a bumb map… Anyway, I want to be able to export CNC data of climbing wall panels so I chose to build my own algorithm for paneling and hole patterns. My algorithm is also capable to create a block of every panel and plane which is amongst other things very useful for mapping textures and exporting geometry for other 3D software.
With hundreds of panels, the production is also a logistical challenge. Panels need to be named with an easily understandeable name. So far I’m using the following format: sector – plane – panel id. Additional metadata such as number of holes, length and angle of cutting operations and color is saved in a spreadsheet.
The general goal of my algorithm is to reduce boring repetitive tasks, avoid mistakes and provide perfect 3D files for climbing wall manufacturers.
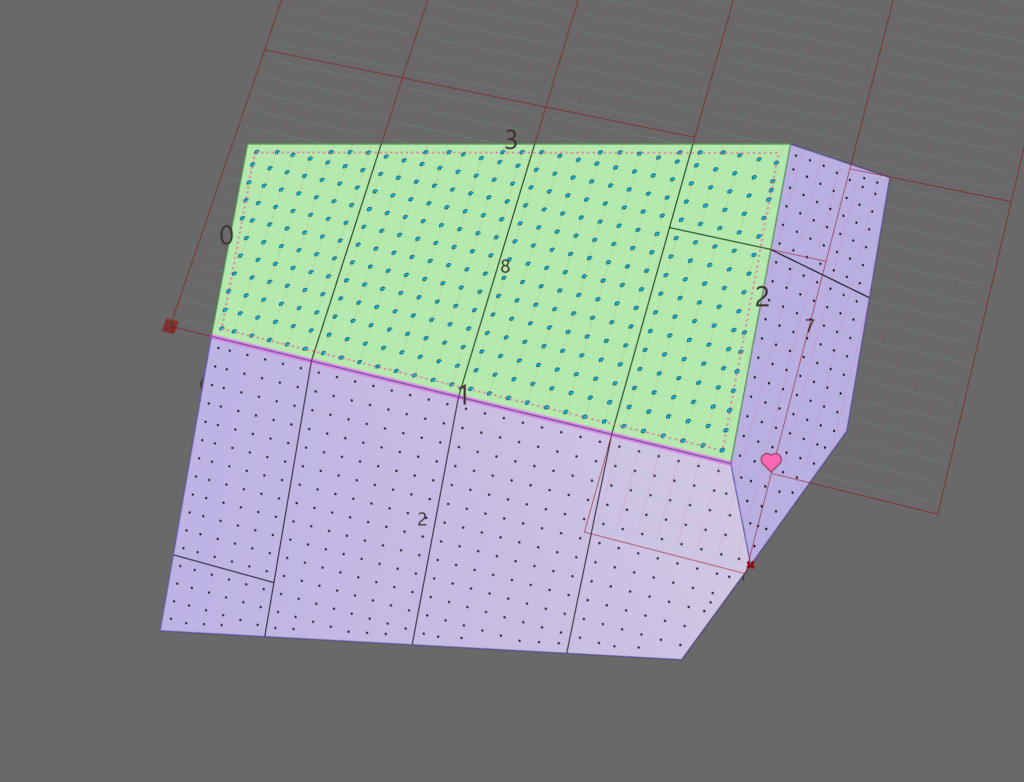
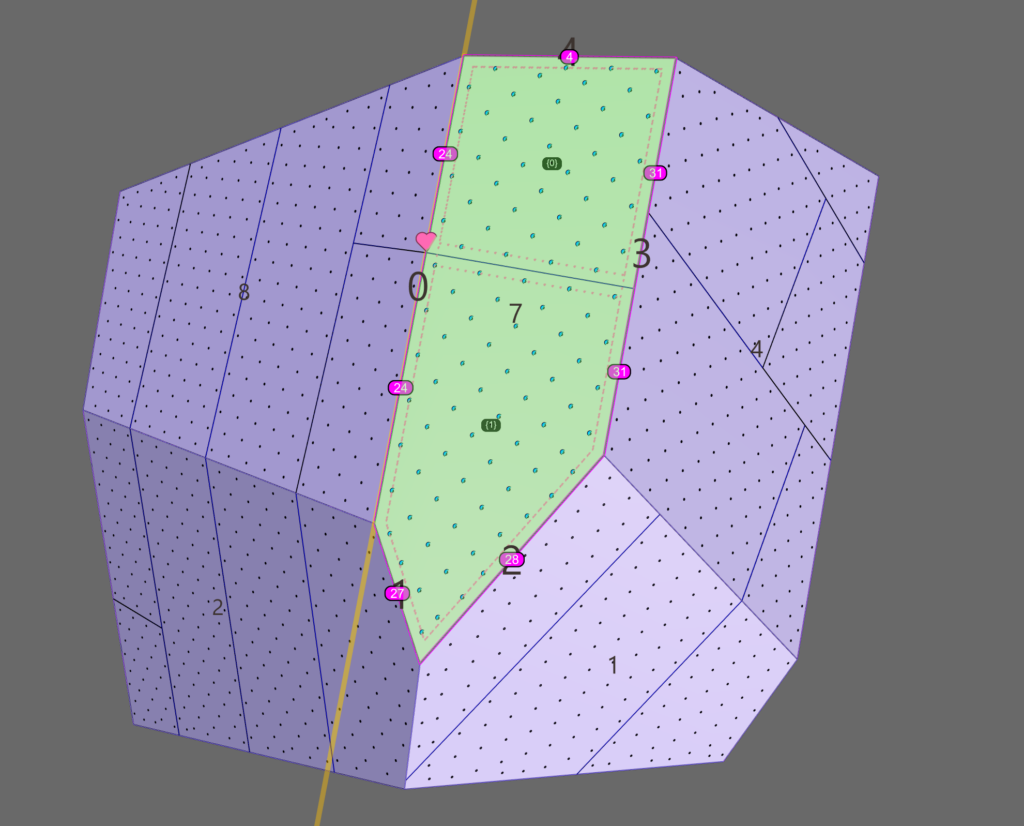
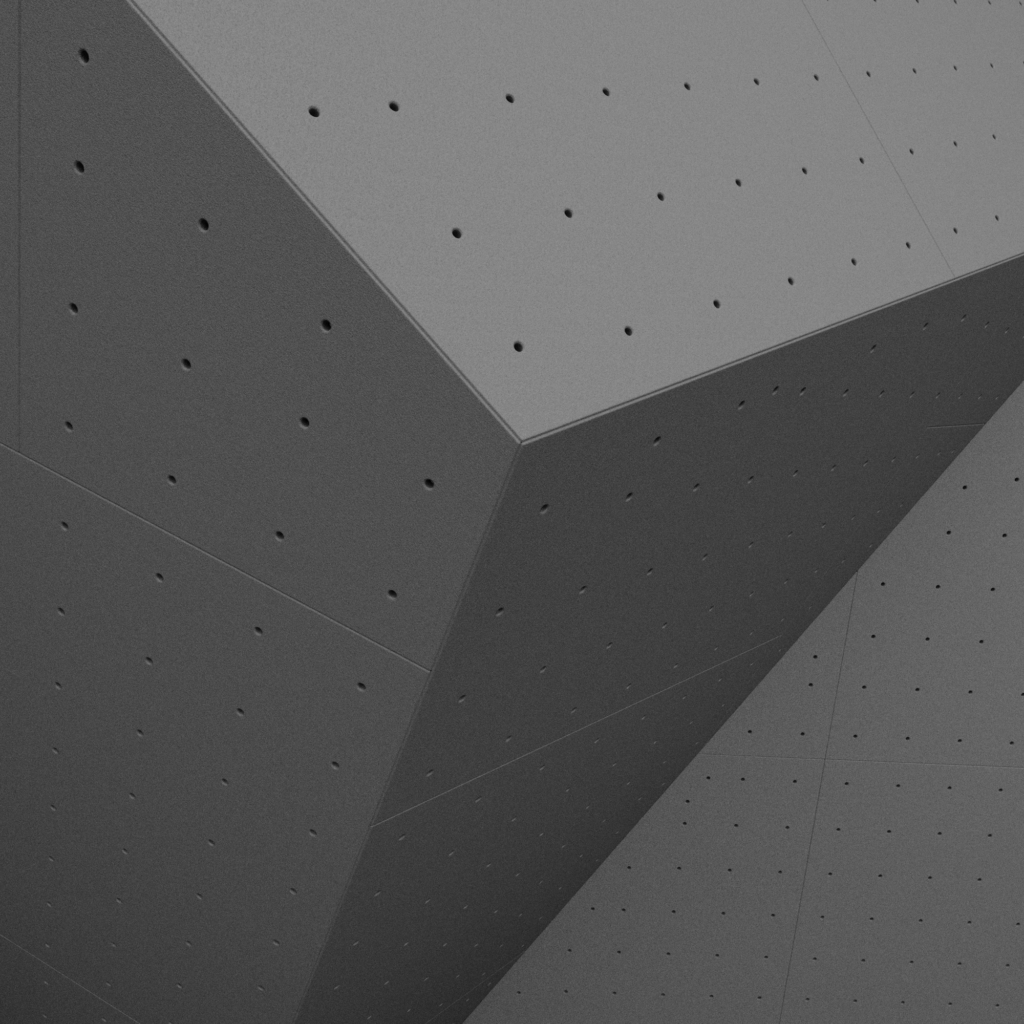
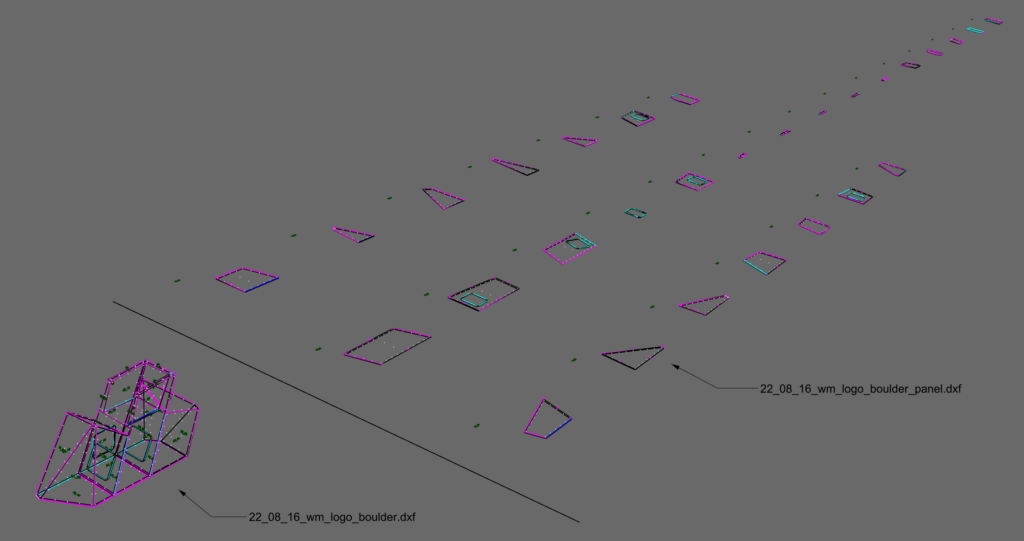
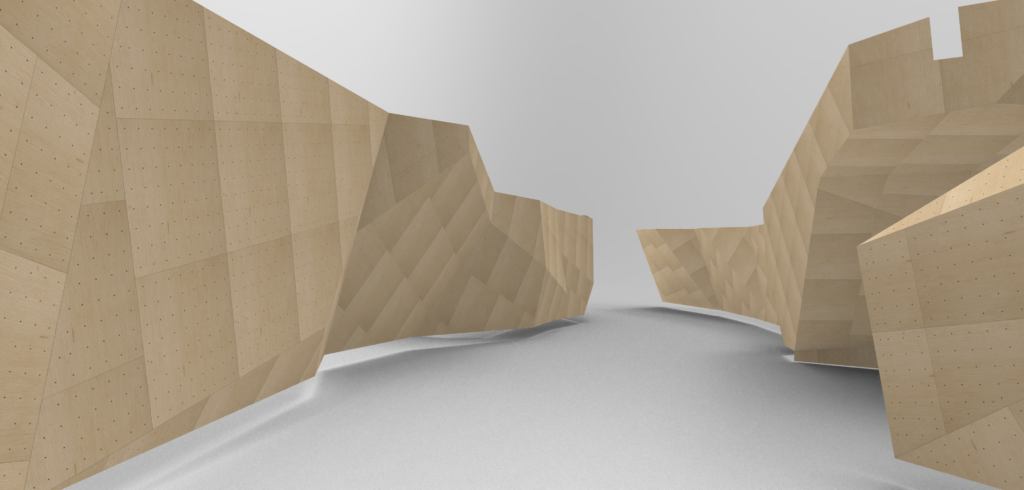